In today’s fast-paced industrial world, downtime is a dirty word. Every minute a machine isn’t running costs money, impacts production, and can even harm your reputation. But what if you could predict failures before they happen, moving beyond reactive fixes to proactive precision? That’s the power of the Internet of Things (IoT) and predictive maintenance, driven by smart data and intelligent insights.
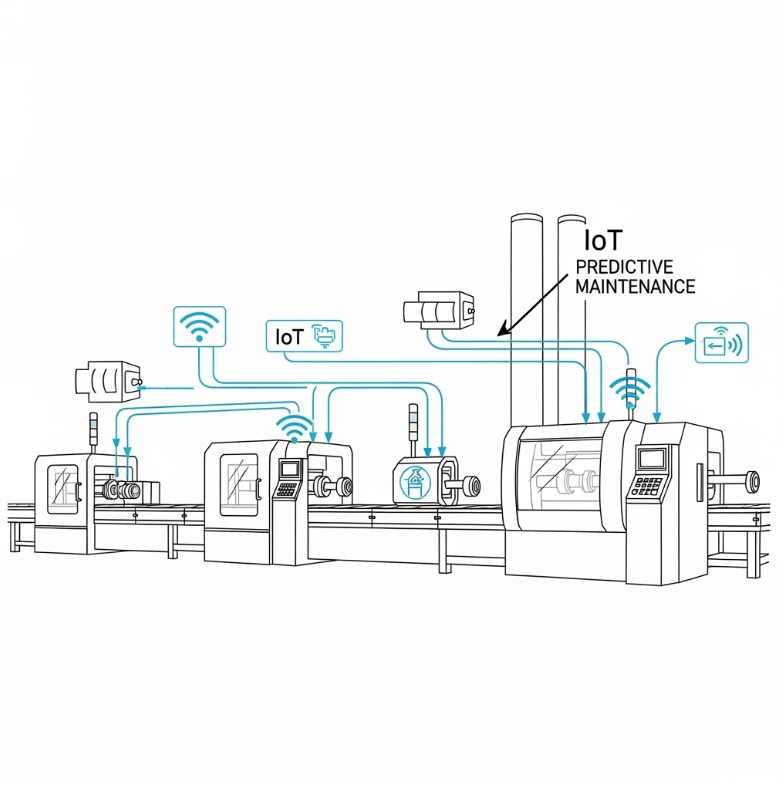
For years, maintenance teams have relied on key metrics to gauge their effectiveness. These Key Performance Indicators (KPIs), tracked by systems like a Computerized Maintenance Management System (CMMS), offer invaluable insights. They help measure everything from repair times to the overall health of your assets. Now, with IoT, these metrics are more powerful than ever, enabling a shift towards true predictive capabilities.
The Metrics That Matter: From Reactive to Predictive Power
Maintenance metrics fall into two main categories:
- Leading indicators are your crystal ball, helping you anticipate future trends and potential issues. Think of them as early warning signs.
- Lagging indicators look at past performance, helping you understand what has happened and how to improve.
The most successful organizations leverage a blend of both. Here are seven crucial metrics, now supercharged by IoT, that are key to a robust predictive maintenance strategy:
1. Mean Time Between Failure (MTBF)
Historically, MTBF told you the average time between breakdowns. With IoT sensors constantly monitoring machine health – vibrations, temperature, pressure – you’re no longer just looking at averages. You’re getting real-time data that can signal impending failure, allowing you to intervene before a complete breakdown. This transforms MTBF from a historical measure into a dynamic indicator for optimizing your preventive maintenance (PM) schedules.
2. Mean Time to Repair (MTTR)
When an issue does occur, every second counts. MTTR measures how quickly you can diagnose and fix a problem. IoT-enabled diagnostics can dramatically reduce this time by providing immediate, precise fault information. Imagine a sensor identifying the exact component failing, allowing your team to arrive prepared with the right tools and parts. This directly impacts your bottom line by minimizing lost production.
3. Inventory Turnover
Efficient inventory management is critical for timely repairs. IoT can connect your spare parts inventory with real-time asset health data. This means your CMMS can automatically trigger reorders for parts predicted to be needed soon, optimizing stock levels and ensuring you have the right components on hand when a predictive maintenance intervention is planned. No more holding excessive stock or scrambling for critical parts!
4. Planned vs. Unplanned Maintenance
This metric traditionally showed your success in scheduling tasks versus reacting to emergencies. With IoT-driven predictive maintenance, the goal is to drastically reduce unplanned maintenance. By anticipating failures, you convert reactive repairs into planned, scheduled activities, minimizing disruption and maximizing efficiency.
5. Planned Maintenance Percentage
A high percentage here indicates a well-oiled maintenance machine. IoT further pushes this by providing the data needed to schedule maintenance precisely when it’s most effective – not too early, not too late. Aim for that “world class” 90%+ by letting real-time data guide your planning.
6. Preventive Maintenance (PM) Compliance
PM compliance measures how well you stick to your schedule. IoT can enhance this by providing more intelligent scheduling. Instead of fixed time-based PMs, you can transition to condition-based maintenance, where tasks are triggered by actual equipment needs, improving both efficiency and compliance. Your CMMS can then track these smart PMs, ensuring they’re completed within optimal windows.
7. Overall Equipment Effectiveness (OEE)
OEE is the ultimate measure of how effectively your equipment is utilized, considering its availability, performance, and quality. IoT sensors feed continuous data into your OEE calculations, giving you an unparalleled, real-time understanding of your assets’ true operational efficiency. This data-driven picture is essential for identifying bottlenecks and optimizing your entire operation to minimize defects and maximize output.
The CMMS: Your Predictive Maintenance Command Center
While IoT sensors gather the raw data, a sophisticated CMMS acts as your central command center, making sense of it all. Modern CMMS solutions are built to integrate seamlessly with IoT devices, collecting, analyzing, and transforming vast amounts of performance data into actionable insights.
With a CMMS, organizations can:
- Monitor a wide range of KPIs in real-time, allowing for immediate responses to developing issues.
- Generate insightful reports and dashboards, providing both quantitative and qualitative views of your maintenance strategy.
- Proactively schedule maintenance based on actual equipment conditions rather than arbitrary schedules.
- Optimize inventory management by anticipating part needs.
By deploying CMMS solutions integrated with IoT, organizations are seeing tangible improvements in MTBF, MTTR, planned maintenance percentages, PM compliance, and OEE. They are shifting from a reactive “fix-it-when-it-breaks” mentality to a highly efficient, data-driven approach that predicts and prevents, keeping operations running smoothly and profitably.
Ready to transform your maintenance strategy from reactive to predictive?