Introduction
In the world of industrial machinery, every hum, every tremor, and every subtle vibration tells a story. For decades, skilled engineers have painstakingly analyzed these mechanical “heartbeats” to predict impending failures, a crucial practice known as predictive maintenance (PdM). But what if we could empower our machines to tell us their stories in a language we intuitively understand, even when the data is ambiguous? Enter Fuzzy Logic, an unsung hero that’s transforming how we approach vibration analysis and prediction.
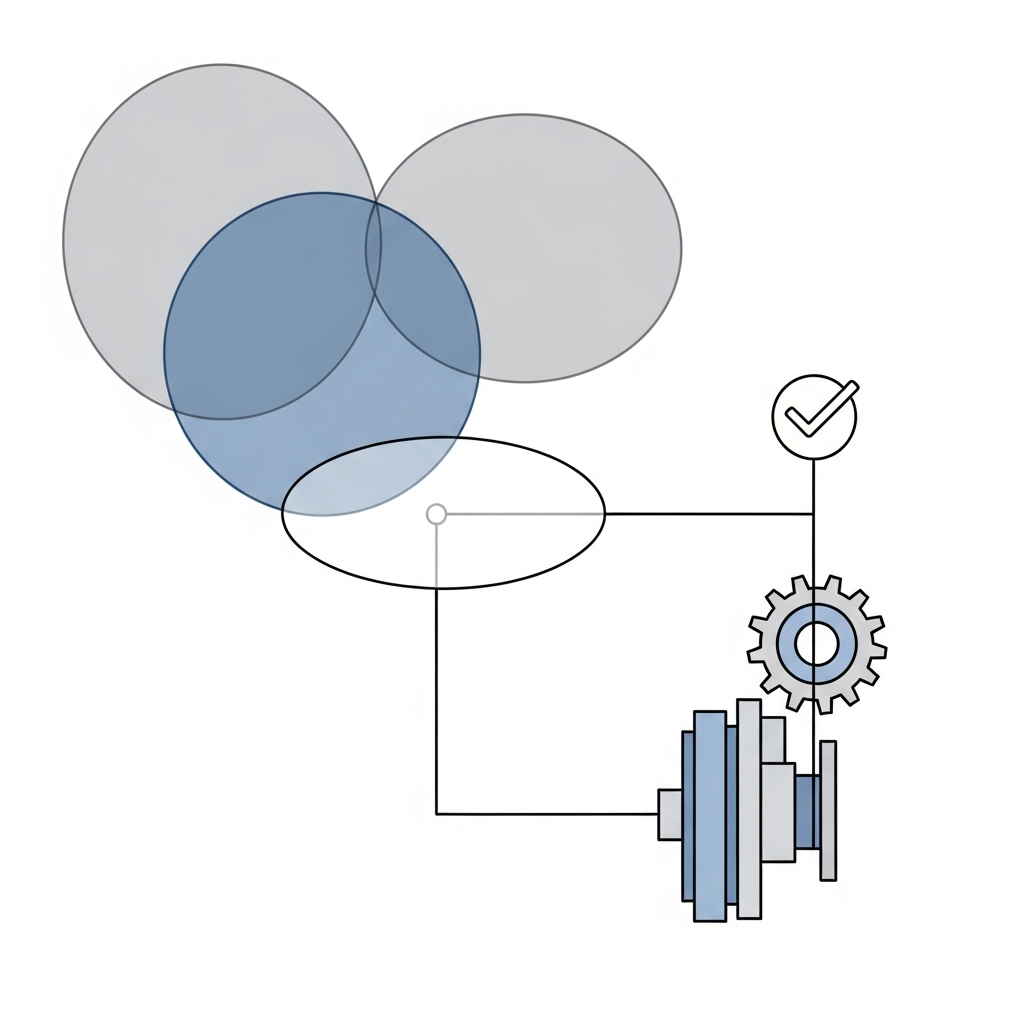
The Challenge of Real-World Data: Why “Black Boxes” Fall Short
Traditional AI and machine learning models have made incredible strides in PdM, accurately forecasting equipment breakdowns. However, they often operate as “black boxes,” providing predictions without clear explanations. In the complex, often imprecise world of machinery vibrations, where a “slightly high” amplitude or a “somewhat irregular” frequency can be critical, this lack of transparency is a significant hurdle. Engineers and maintenance teams need to understand why a machine is predicted to fail to truly trust the system and take effective, targeted action.
This is where Explainable Artificial Intelligence (XAI) comes into play, and within XAI, Fuzzy Logic stands out for its remarkable ability to bridge the gap between complex data and human understanding.
Fuzzy Logic: Speaking the Language of Imprecision
Unlike conventional “crisp” logic, which operates on strict true/false or 0/1 values, fuzzy logic embraces the nuances of real-world data. It allows for degrees of truth, enabling systems to reason with concepts like “high,” “low,” “warm,” or “fast” – terms that are inherently imprecise but commonly used in human assessment.
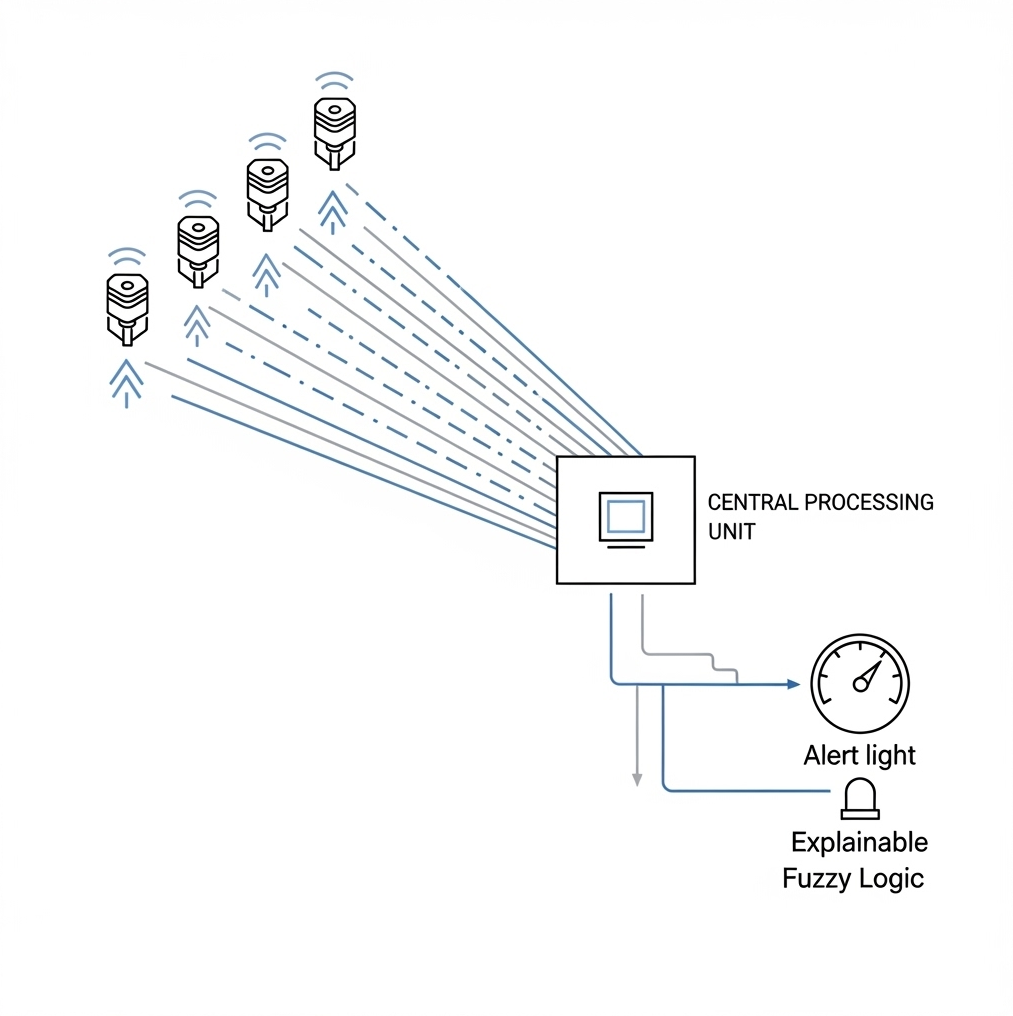
At its core, fuzzy logic utilizes Fuzzy Inference Systems (FIS), which are built upon fuzzy rules. These rules are expressed as intuitive “IF-THEN” statements, mirroring human decision-making processes.
Imagine a fuzzy rule for vibration analysis:
- IF (Vibration Amplitude is Medium-High) AND (Dominant Frequency is Near Bearing Natural Frequency), THEN (Likelihood of Bearing Wear is Elevated).
This simple rule demonstrates the power of fuzzy logic:
- Human-Like Reasoning: It uses linguistic terms that engineers and technicians already use to describe machine conditions. This makes the AI’s logic immediately comprehensible.
- Handling Ambiguity: “Medium-High” and “Near Bearing Natural Frequency” are not exact numbers but ranges, allowing the system to handle the inherent imprecision and variability of real-world vibration data.
- Transparency: The “IF-THEN” structure clearly lays out the conditions leading to a particular conclusion, eliminating the “black box” mystery.
How Fuzzy Logic Enhances Predictive Maintenance for Vibrations
By integrating fuzzy logic into vibration analysis, we unlock several key advantages for PdM:
- Enhanced Interpretability: Fuzzy rules provide a clear, human-readable explanation for predictions. This builds trust and confidence among maintenance personnel, encouraging them to act on AI-driven insights.
- Robustness to Noisy Data: Industrial environments are rarely pristine. Fuzzy logic’s ability to handle imprecise and uncertain inputs makes it more resilient to the noise and variability often found in vibration data.
- Integration of Expert Knowledge: Fuzzy rules can be directly formulated from the invaluable experience of seasoned vibration analysts. This allows for a powerful synergy between human expertise and data-driven insights.
- Adaptive Learning: Advanced fuzzy systems, like Adaptive Neuro-Fuzzy Inference Systems (ANFIS), can learn and optimize their fuzzy rules and parameters directly from historical vibration data, continuously improving their predictive accuracy while retaining interpretability.
- Actionable Insights: When a fuzzy logic system predicts a potential issue, it can explain why based on understandable linguistic terms. This empowers maintenance teams to quickly identify the likely root cause and plan targeted interventions, minimizing downtime.

Beyond the Hype: Practical Applications
Consider a scenario where a motor’s vibration data is being monitored. A fuzzy logic-based PdM system might process this data and generate an alert, explaining: “Based on the slightly elevated vibration levels at the inner race frequency, there is a moderate risk of inner bearing degradation.”
This level of detail and clarity is invaluable. It allows the maintenance team to:
- Prioritize inspections.
- Order specific replacement parts.
- Schedule maintenance during planned downtime, avoiding costly emergency repairs.
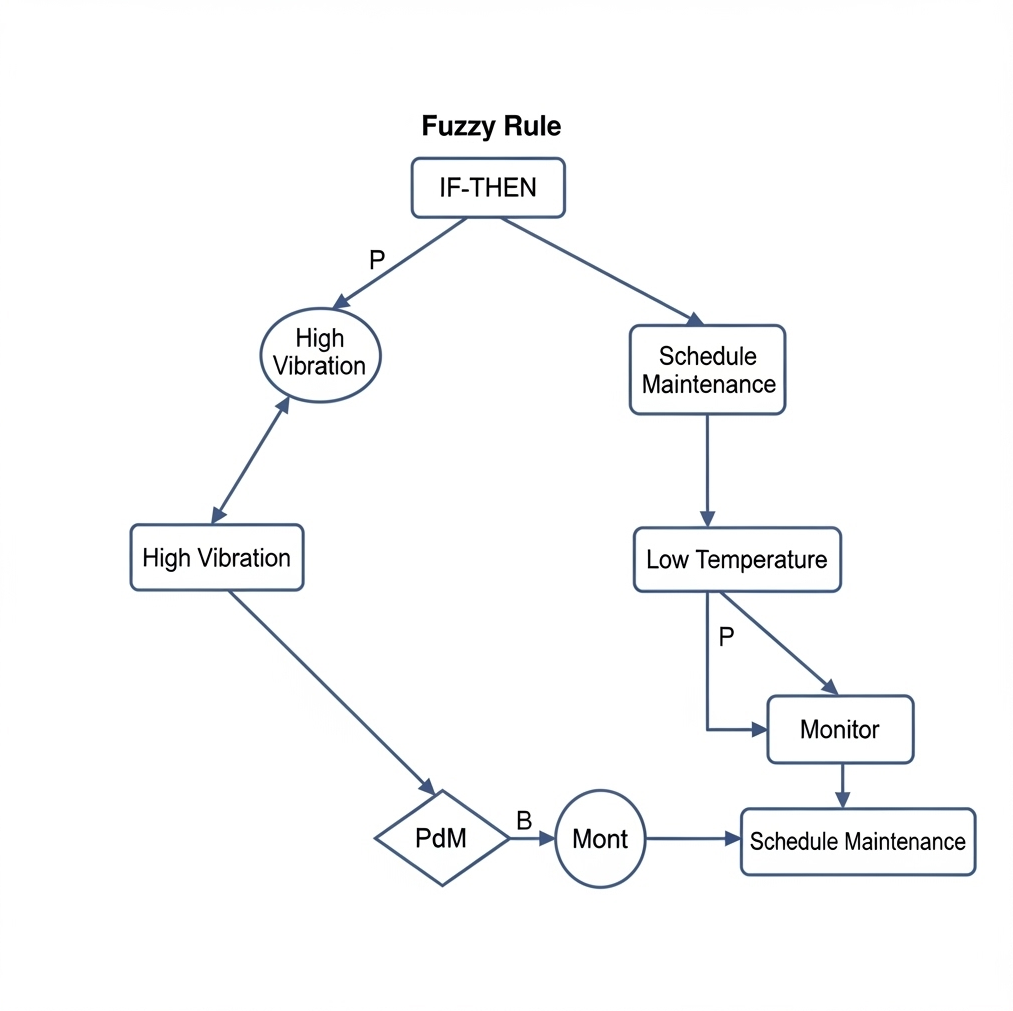
The Future is Fuzzy and Transparent
As industries continue to embrace digitalization and seek greater efficiency, the demand for transparent and trustworthy AI solutions will only grow. Fuzzy logic, with its unique ability to combine the power of AI with human-like reasoning, is poised to play a pivotal role in the evolution of predictive maintenance for machinery vibration analysis. It’s not just about predicting failures; it’s about understanding them, and that understanding is the key to a more reliable and efficient industrial future.
Let’s connect with us on vibration analysys subjects and design your own dedicated Fuzzy Logic PmD solution!