To line managers in bustling plants and dedicated automation maintainers in factories with years of history, the idea of “predictive maintenance” might sound like something out of a futuristic movie. You’re likely adept at managing breakdowns, optimizing preventive schedules, and squeezing every ounce of life out of your valuable machinery. You probably rely heavily on your Computerized Maintenance Management System (CMMS) for tracking work orders, managing inventory, and understanding maintenance history.
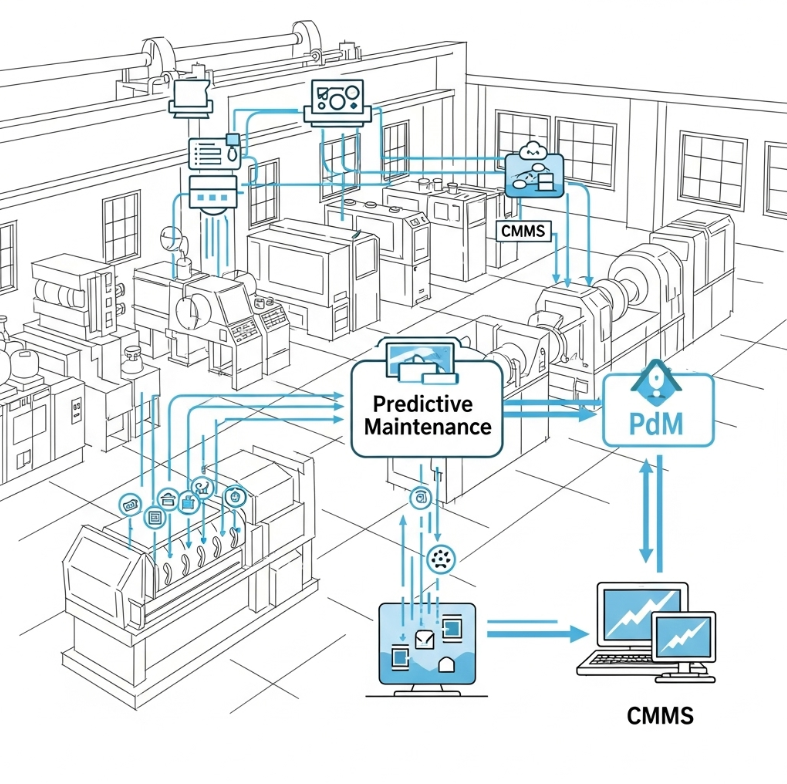
But what if your CMMS could do more than just record the past and organize the present? What if it could predict the future? The good news is, it can. The evolution of CMMS software is not about replacing what you know, but about supercharging it, transforming your maintenance strategy from a necessary expense into a powerful competitive advantage.
The Shift: From CMMS as a Record-Keeper to a Predictive Powerhouse
Historically, a CMMS has been your maintenance team’s central nervous system. It handles work orders, asset tracking, spare parts management, and preventive maintenance scheduling. This foundation is invaluable. However, traditional CMMS often operates on a reactive or time-based preventive model. You fix things when they break, or you service them at set intervals, regardless of their actual condition.
Predictive Maintenance (PdM) changes the game. Instead of relying on guesswork or fixed schedules, PdM uses real-time data from sensors (part of the Internet of Things, or IoT) to monitor the actual health and performance of your machines. This data, when analyzed by advanced algorithms (often powered by AI and machine learning), allows you to anticipate potential failures before they occur.
The exciting news for older or mid-age factories is that you don’t need to rip out your existing CMMS and start from scratch. Modern CMMS solutions are designed to integrate seamlessly with these new predictive capabilities. Your CMMS becomes the brain that processes the insights from your IoT sensors, automatically generating intelligent work orders when anomalies are detected.
Why This Matters for You: Tangible Benefits on the Plant Floor
As a line manager or automation maintainer, you face daily challenges: unexpected downtime, costly emergency repairs, missed production targets, and the constant pressure to optimize resources. Predictive maintenance, powered by an evolved CMMS, directly addresses these pain points:
- Drastically Reduced Unplanned Downtime: This is the big one. Imagine a vibration sensor on a critical pump detecting a subtle change that indicates bearing wear, weeks before a catastrophic failure. Your CMMS receives the alert, automatically creates a work order, and you schedule the repair during a planned downtime or off-shift. No sudden stoppage, no scrambling, no lost production.
- Positive Example: A major automotive plant implemented PdM on their welding robots. They found that by monitoring motor vibrations, they could predict and replace failing components during scheduled breaks, reducing unplanned line stops by over 60%.
- Optimized Maintenance Costs: Reactive maintenance is expensive. Emergency repairs often involve overtime, expedited parts shipping, and longer downtime. Preventive maintenance, while better, can lead to “over-maintenance” – replacing parts that still have life in them. PdM ensures you fix things only when they need fixing, saving on labor, parts, and reducing unnecessary interventions.
- Positive Example: A food processing facility used thermal imaging sensors on their refrigeration units. Their CMMS analyzed the temperature data, allowing them to identify and address minor heat issues before they escalated into major compressor failures, leading to a 25% reduction in annual maintenance spend on those units.
- Extended Asset Lifespan: By catching small issues before they become big problems, you prevent cumulative damage to your equipment. This means your valuable machinery lasts longer, delaying costly capital expenditures for replacements.
- Positive Example: A packaging manufacturer started monitoring the hydraulic systems of their older filling machines with pressure sensors. Early detection of minor leaks and pressure drops, managed through their CMMS, helped them extend the operational life of these machines by several years, postponing significant investment in new equipment.
- Improved Safety: Predicting failures reduces the risk of dangerous breakdowns. If a machine unexpectedly seizes or a component breaks mid-operation, it can pose significant safety hazards. PdM allows for controlled, scheduled interventions, creating a safer working environment for your team.
- Better Resource Allocation: With fewer emergencies, your skilled technicians can shift their focus from firefighting to more strategic, value-adding activities. Your spare parts inventory can be optimized, reducing carrying costs while ensuring availability for predicted needs.
How to Get Started in Your Factory
You might be thinking, “My machines are old. We don’t have fancy sensors.” That’s okay! Implementing predictive maintenance doesn’t require a complete overhaul overnight. Here’s a realistic approach:
- Start Small, Think Big: Identify your most critical assets – the machines that would cause the most pain if they went down. These are your prime candidates for a pilot PdM program.
- Leverage Your CMMS: Talk to your CMMS provider. Many modern CMMS platforms offer integration capabilities or modules specifically designed for condition monitoring and predictive analytics. Your existing system can become the hub for new sensor data.
- Sensor Retrofitting: Older machines can often be retrofitted with cost-effective, non-invasive sensors (e.g., vibration, temperature, acoustic, current sensors). These “plug-and-play” devices are becoming increasingly affordable and easy to install.
- Data Analysis & Training: You don’t need to become a data scientist. Many CMMS platforms now have built-in analytics and user-friendly dashboards that translate raw sensor data into actionable insights. Training your maintenance team to interpret these insights is key.
- Phased Implementation: Don’t try to change everything at once. Implement PdM on a few critical assets, learn from the experience, demonstrate ROI, and then gradually expand across your facility.
The future of maintenance is here, and it’s built on intelligence, not just reaction. By embracing the evolution of your CMMS and integrating predictive maintenance solutions, you’re not just preventing breakdowns; you’re building a more efficient, safer, and ultimately more profitable factory. It’s time to inspire your plant into the predictive age!